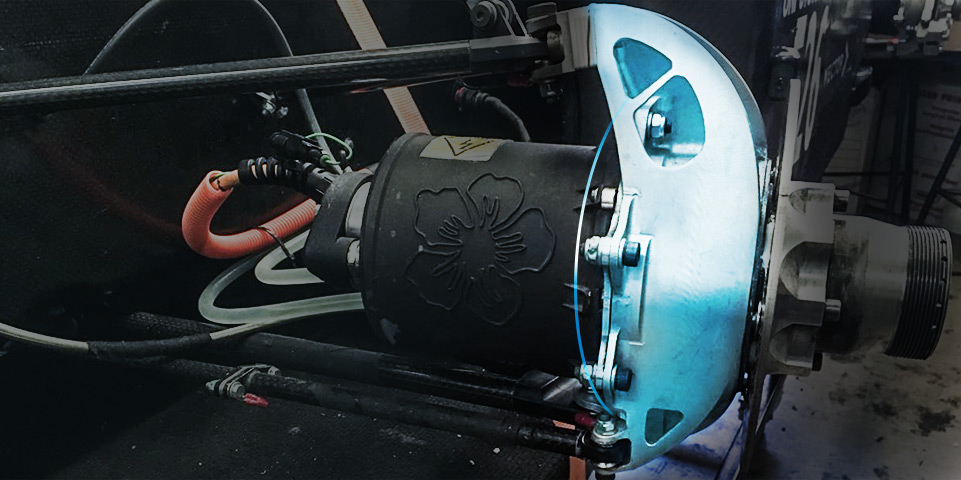
1Konzept Green Team
Die Auslegung der Radträger des Green Team E8
https://www.greenteam-stuttgart.de erfolgte als Vollfräsbauteil. Obwohl Vollfrästeile ja nichts Neues sind, ist mit dem alten Motorsportstandard ein Gewicht von 400 Gramm vorne und 420 Gramm hinten zu realisieren. Die geringen Gewichte wurden durch sehr dünnen Wandstärken und die Verwendung von EN-AW7075 erreicht. Hier haben wir ebenfalls alle wichtigen Merkmale in einer Aufspannung gefertigt, das Konzept erfordert ja die gleichen Toleranzen für Radlager und Getriebe.
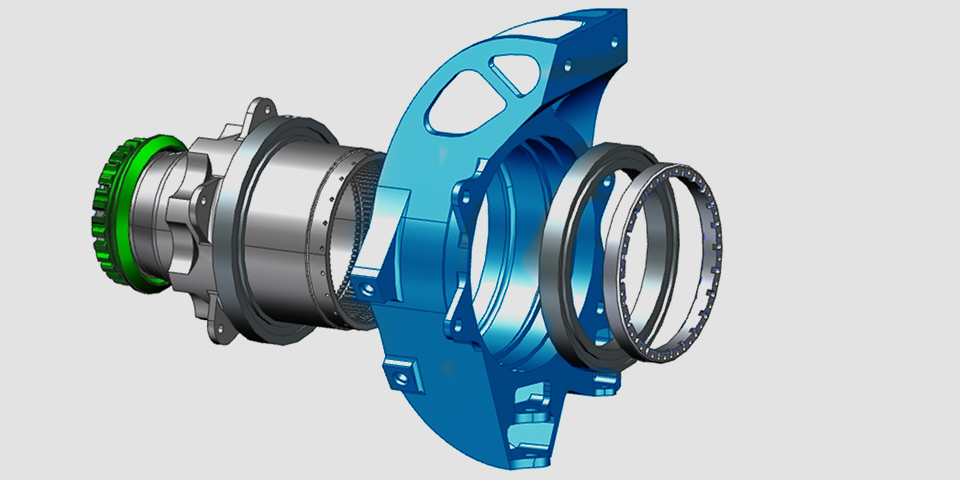
2Umsetzung
Bei Vollfrästeilen sind Probleme sehr viel einfacher wieder zu korrigieren. Nach Abstellen des Fehlers, können wir einfach ein weiteres Bauteil fräsen. Entgegen der additiv gefertigten Bauteile oder Gussteile, benötigt man in den meisten Fällen keine Vorrichtung. Für die Radträger wurde jedoch hier eine zweite Aufspannung benötigt. Die CAM Programmierung ist aufwendiger als bei der Fertigung mit einem Guss- oder additiven Rohteil. Im Vergleich zu Guss ist der Break-even meist bei ca. 10 Teilen. Bei unter 10 Teilen ist die Fertigung aus dem Vollen also immer die kostengünstigste Möglichkeit.
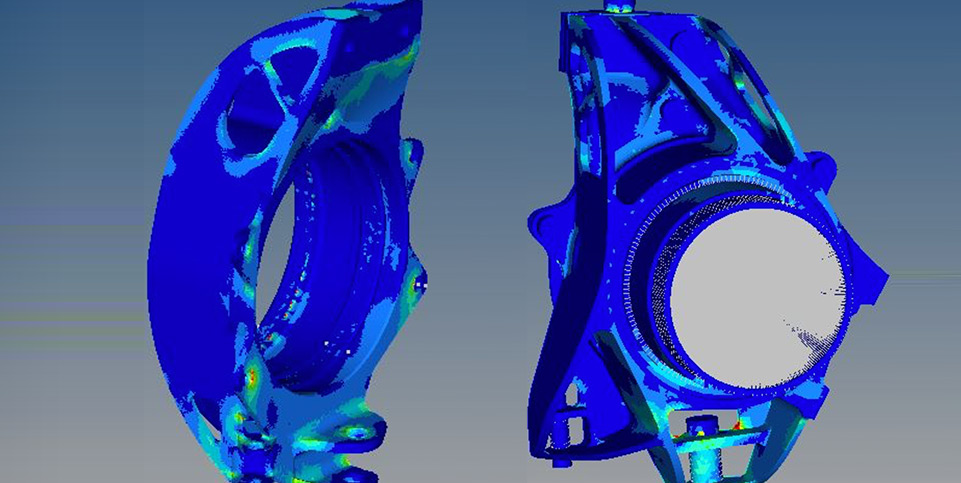
3Time to Market
Vollfrästeile auch in hoher Komplexität oder Stückzahl sind die tatsächlichen Favoriten im Rennen wenn es um die Lieferzeit geht. Hier ist unser Standard 2 Kalenderwochen. Wenn wir die gewünschte Legierung lagernd haben, können wir auch mal deutlich schneller aushelfen. So ergibt es sich auch, dass wir hier bei Problemen oder benötigtem Ersatz oft mit Zeiten von unter 1 Kalenderwoche trumpfen können.
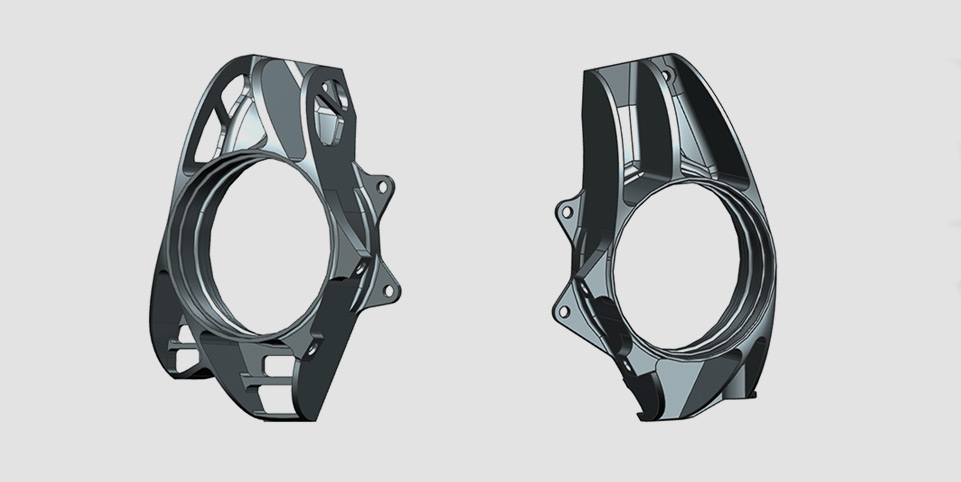
4Kosten
Beim Thema Kosten hat das Vollfrästeil einen klaren Sieg eingefahren. Bei genauer Untersuchung fällt auf, dass man zwar ein aufwendigeres CAM-Programm benötigt, dafür jedoch die Positionenvorrichtung und additives Rohteil einspart. Man benötigt natürlich auch ein Rohteil, der volle Aluminium Klotz ist jedoch weder von der Optik noch vom Preis mit der additiven Variante zu vergleichen. So fiel die längere Laufzeit auf der CNC Maschine auch nicht ins Gewicht. Durch den Einsatz modernster Technologie haben wir den Klassiker im Prototypensegment fit für die Zukunft gemacht.
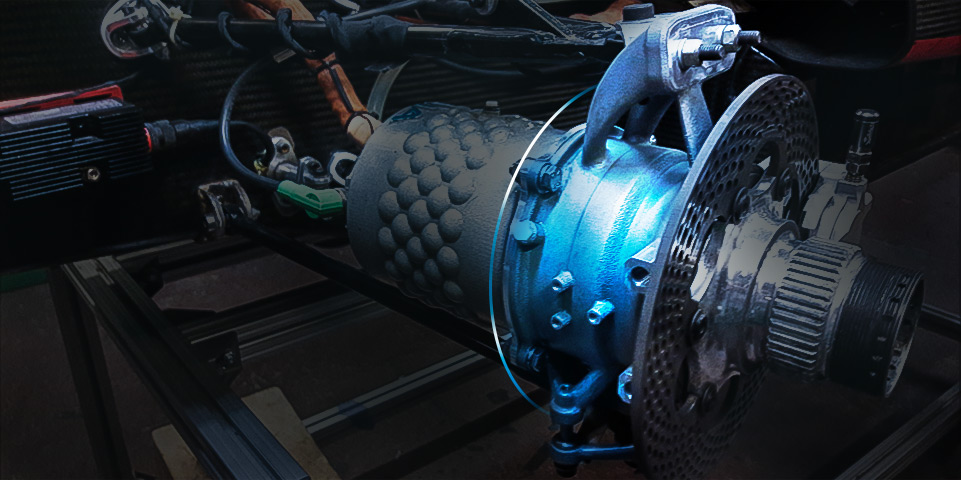
1Konzept DHBW
Die Auslegung der Radträger des DHBW eSleek17
https://dhbw-engineering.de erfolgte als additiv gefertigter Bauteile. Durch die Form die aus einer Topologieoptimiertung resultiert und keine Rücksicht auf die Fräsbarkeit nehmen musste, wurde ein Gewicht von 530 Gramm vorne und 460 Gramm hinten realisiert. Die Rohteile wurden von Protolaps aus AL-Si10Mg gefertigt. Additiv gefertigte Bauteile können aber natürlich auch von uns bezogen werden. Durch die Fertigung aller wichtigen Merkmale in einer Aufspannung konnten die sehr kleinen Toleranzen für die Radlager und die Aufnahme des Planetengetriebes realisiert werden. Dafür war jedoch eine aufwendige Vorrichtung je Radträger notwendig um die Rohteile aufnehmen zu können.
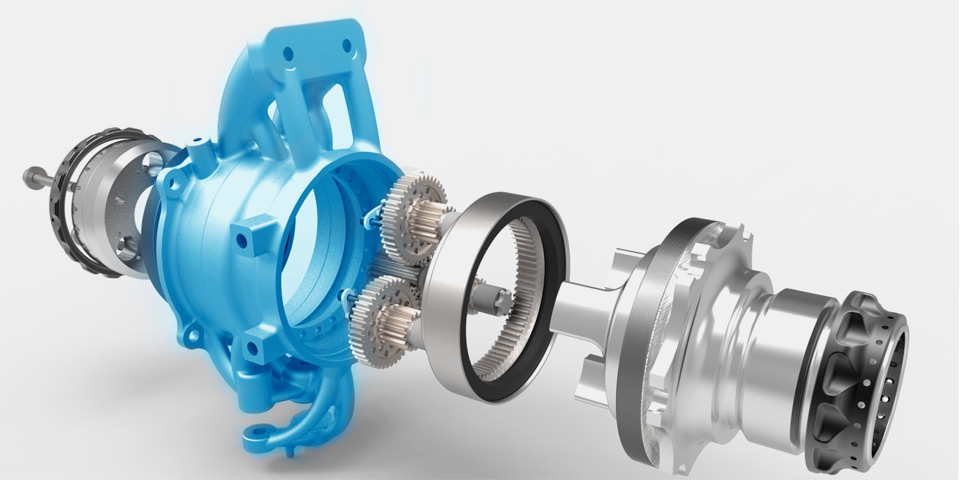
2Umsetzung
Die Bearbeitung der engen Toleranzen ist für uns kein Problem, Konzentrizitäten < 0,05mm und Passungen mit Toleranzen < 0,01mm sind unser tägliches Geschäft. Daher unterstützen wir das Team gerne mit der mechanischen Bearbeitung. Bei additiven Bauteilen kommt jedoch die Programmierung der Konstruktion, Programmierung und Fertigung der Vorrichtung, zusätzlich zur Bauteil Programmierung und Fertigung hinzu. Zusätzliche Probleme sind, dass normalerweise keine Einfahrteile vorhanden sind, wie in diesem Fall auch. Daher sind die Preise für die mechanische Bearbeitung oft höher, beziehungsweise manche Unternehmen bearbeiten solche Teile gar nicht.
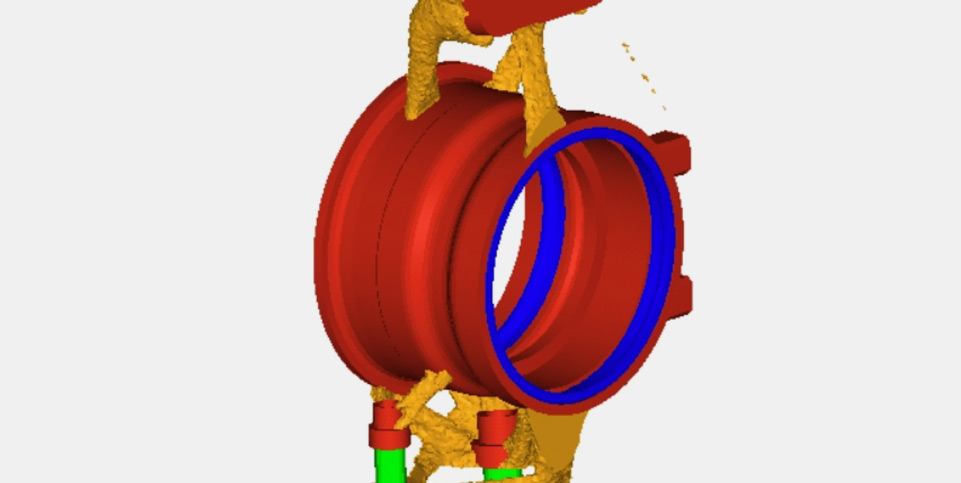
3Time to Market
Die Terminschiene wird allgemein bei additiv gefertigten Teilen als kurz beschrieben. Bei genauer Betrachtung notierten wir folgendes: Fertigung der Rohteile ca. 2 KW, spanende Bearbeitung der Bauteile ca. 1,5 KW. Bei komplexen Bauteilen ist als durchschnittlich von 3,5 KW auszugehen. Es gibt wenige Anbieter die hier die volle Prozesskette abbilden, daher ist deren Flexibilität oft doch nicht so groß wie erwartet.
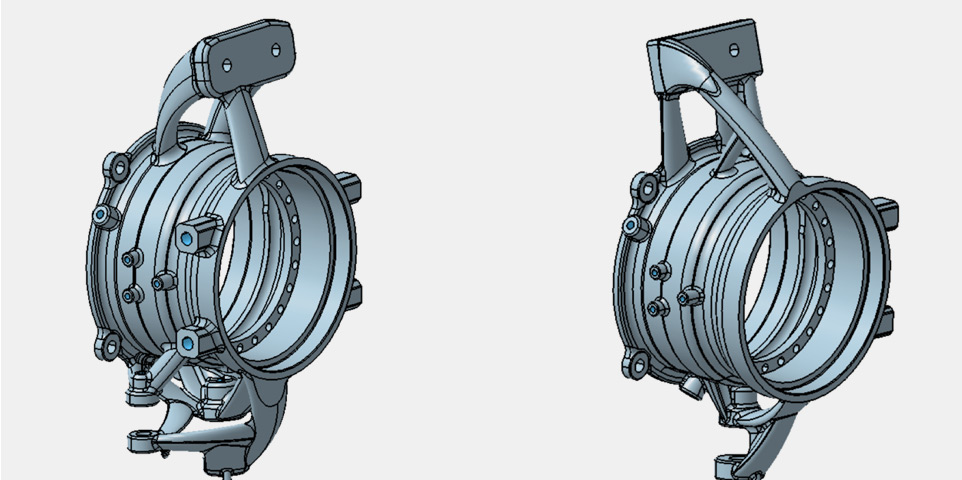
4Kosten
In diesem Referenz Projekt wo sich die Technologien im selben Anwendungsfall exakt vergleichen lassen kommen wir auf Mehrkosten von 39% für die additiv gefertigten Bauteile. Bei genauer Betrachtung liegt die sogar bei der Stückzahl 1 klar auf der Hand. Obwohl wir selbst oft höheren bei geringen Stückzahlen, wäre die additive Fertigung bevorteilt. Wenn man sich aber vor Auge führt, dass man ein sehr teures Rohteil benötigt, eine Vorrichtung, vor und Nachbearbeitung inkl. 2 Vermessungen um kein Rohteil falsch zu bearbeiten, wird der Mehraufwand schnell deutlich. Sollte sich ein Bearbeiter dieses Risiko noch bezahlen lassen ist die Differenz auch schnell mal bei über 60-70%. Die additive Fertigung ist also immernoch erst bei Hybrid-Bauteilen, Konturnaher Kühlung, im Formenbau oder extremer Bauteil Geometrie die perfekte Wahl.